Another study, a collaboration between Freeman Technology and 3P Innovation using dynamic testing to elucidate dosator performance, has demonstrated the relevance of both AE and SE to the choice of optimal dosing equipment, which can be complicated due to conflicting requirements. On one hand, filling the dosator tube calls for a relatively free-flowing powder; on the other hand, formation of a stable powder plug that will remain securely locked in the tube during transfer calls for a certain degree of cohesivity (Figure 4).
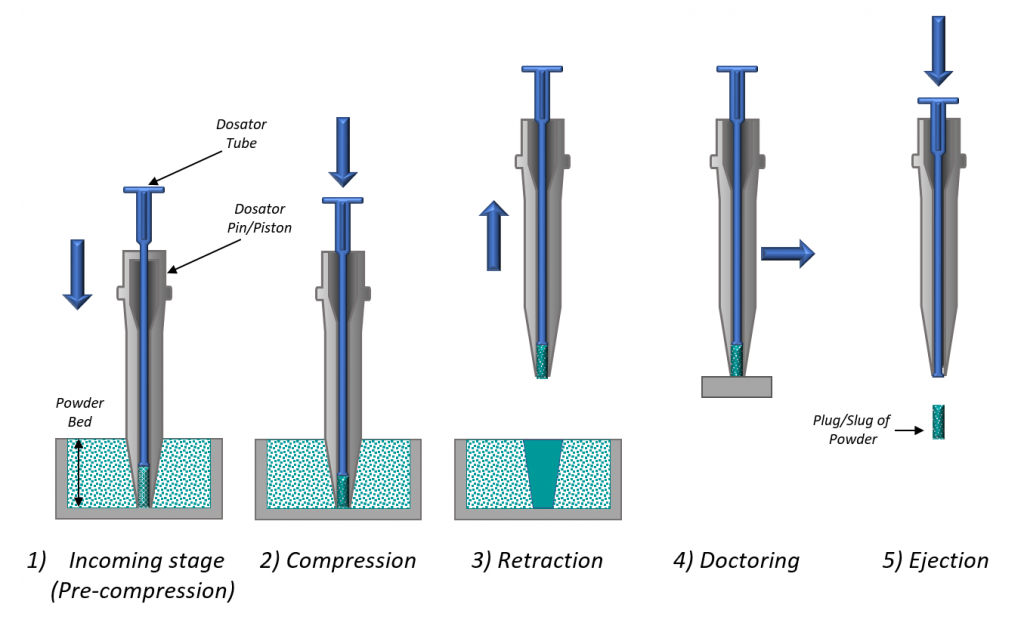
In this study, researchers processed five lactose powders with a lab-scale dosator using outlets of progressively decreasing size, from dosator 1 to dosator 4, and quantifying dosator performance in terms of percent relative standard deviation (RSD) with the aim of consistently producing doses of 50 mg with an RSD of <2%. The researchers also measured dynamic powder properties, notably AE and SE, for each lactose sample and correlated those properties with dosator performance, to investigate the feasibility of matching a formulation with a specific dosator configuration.
D50 Particle Size Range, µm | Dosator 1 | Dosator 2 | Dosator 3 | Dosator 4 | |
Lactose 1 | 180-250 | 2.27 | 2.4 | 2.06 | 0.89 |
Lactose 2 | 110-155 | 3.77 | 1.54 | 1 | 1.08 |
Lactose 3 | 70-110 | 1.84 | 0.85 | 0.79 | 0.56 |
Lactose 4 | 40-70 | 1.34 | 2.02 | 2.13 | 4.41 |
Lactose 5 | 4-11 | 3.76 | 7.05 | 7.59 | 8.32 |
Table 1: Dosator trial data (expressed as %RSD) show how different lactose grades vary in terms of their performance with dosators of different diameter.
For example, the results show that only lactoses 3 and 4, which each have a relatively low AEin combination with a low to mid-range SE, deliver acceptable performance with the largest diameter dosator. Lactose 5 has a low AE; however, the greater mechanical interaction indicated by its high SE appears to compromise performance. On the other end of the spectrum, SE appears to define performance with minimal contribution from AE for the smallest diameter dosator, and lactose 1,2 and 3 all have sufficiently low SE values to perform well on dosator 4.
More generally, the results show that powders with both relatively low AE and SE performed relatively well in all dosator configurations. Powders with a high SE performed particularly poorly with small diameter systems, while AE exhibited greater influence in larger diameter dosators.
While DPI developers naturally focus primarily on ensuring that the formulation will disperse sufficiently well under the prevailing conditions for a given device and on driving up the efficiency of drug delivery by maximizing the fine particle dose, these studies suggest that doing so may result in a formulation with cohesive properties that may be problematic for dosing. In such cases, complementary studies of manufacturing performance with dynamic powder testing methods may help to rapidly and effectively identify the most effective dosing technology to handle the chosen formulation, thereby avoiding manufacturing problems that could increase the time and cost of pilot trials.