When it comes to drug delivery, however, the powder undergoes an aeration, subjecting it to very different stresses than those applied during manufacturing. The flowability characteristics of interest are defined by how the formulation responds to air, and the defining requirement for a dry powder inhaler (DPI) formulation is that the active must disperse to a respirable size during product use. For most DPI devices, dispersion is driven by air drawn through the powder plug during inhalation, thereby creating a differential pressure/velocity profile across the powder bed.
Why are USP tests not sufficient?
Attempts to predict powder behavior from properties measured under conditions that differ significantly from conditions applied during testing may produce unreliable results, so a testing technique that simulates the conditions the powders experience in the process or application of interest can be substantially more valuable.
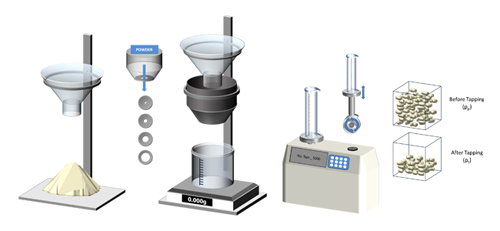
USP methods for powder testing include shear testing, angle of repose, flow through an orifice, and tapped density (Carr’s Compressibility Index/Hausner Ratio) (Figure 2). Of these, only shear testing provides any capability to modify test conditions to ensure relevance to a specific application, although shear tests lack the ability to test powders in a controlled low stress or aerated state, which is particularly relevant for DPIs.
In addition, the tests described in the USP attempt to capture the complexity of powder behavior with a single number, but we generally find that multiple parameters are necessary to robustly define a powder as being suitable or otherwise for a specific application. A powder with a Hausner ratio of between 1.19 and 1.25, for example, is classified as exhibiting fair flow properties, but what does this mean in terms of how the formulation will disperse when aerated or whether there will be sufficiently cohesivity to form a stable plug in a manufacturing process?
Furthermore, shear cell testing aside, the USP methods, which are traditional, largely manual procedures with arguably poorly defined methods, tend to exhibit relatively poor repeatability and reproducibility. As a result, these methods have a limited ability to differentiate similar samples, which is a major limitation when trying to optimize a formulation against demanding constraints.